Unleashing the Potential of Chemical Filter Plates in Industrial Applications
Jul 02,2025
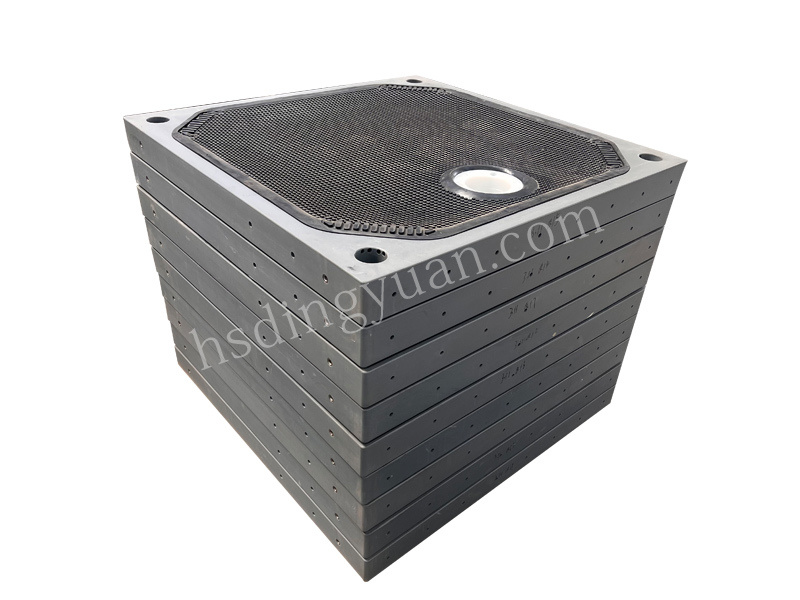
Unleashing the Potential of Chemical Filter Plates in Industrial Applications
Table of Contents
- Introduction to Chemical Filter Plates
- Understanding the Importance of Filtration in Industrial Processes
- Key Features of Chemical Filter Plates
- Various Industrial Applications of Chemical Filter Plates
- Advantages of Using Chemical Filter Plates in Industrial Settings
- Maintenance and Care for Chemical Filter Plates
- Future Trends and Innovations in Filter Plate Technology
- Frequently Asked Questions
- Conclusion
Introduction to Chemical Filter Plates
Chemical filter plates are integral components in various industrial processes, designed to separate solids from liquids efficiently. These plates are utilized in multiple sectors, including pharmaceuticals, chemical manufacturing, food processing, and wastewater treatment. The design and materials used in chemical filter plates enable them to withstand harsh environments, making them indispensable for maintaining production efficiency and product quality.
Understanding the Importance of Filtration in Industrial Processes
Filtration plays a critical role in industrial applications, ensuring the purity of end products while protecting equipment from contamination. Effective filtration minimizes downtime and maintenance costs, contributing to overall operational efficiency. Chemical filter plates are specifically engineered to optimize these processes by providing a reliable and consistent means of separating unwanted particulates from valuable liquids.
Enhancing Product Quality
One of the primary goals of filtration is to enhance product quality. In industries such as pharmaceuticals and food processing, even minor contaminations can lead to significant health risks and financial losses. Chemical filter plates serve as a barrier, ensuring that only the desired liquids pass through, thus safeguarding product integrity.
Regulatory Compliance
Many industries are governed by strict regulations regarding product purity and environmental impact. The use of effective filtration systems, such as chemical filter plates, helps companies comply with these regulations, avoiding penalties and enhancing their reputation in the market.
Key Features of Chemical Filter Plates
Chemical filter plates are engineered with several key features that enhance their performance and durability.
Material Composition
The materials used in the construction of chemical filter plates significantly influence their functionality. Common materials include polypropylene, polyethylene, and stainless steel. Each material has distinct advantages, such as chemical resistance, temperature tolerance, and durability.
Design Efficiency
The design of chemical filter plates is tailored to maximize filtration efficiency. Features such as tapered edges and optimized pore sizes ensure that solids are effectively captured while allowing liquids to flow freely. Additionally, modern designs often incorporate innovative technologies that enhance their filtering capabilities.
Easy Integration
These filter plates are designed for seamless integration into existing systems. Their standard dimensions and configurations make them compatible with most filtration equipment, simplifying the installation process and reducing the need for extensive modifications.
Various Industrial Applications of Chemical Filter Plates
Chemical filter plates find applications across a broad spectrum of industries. Below are some notable examples:
Pharmaceutical Industry
In the pharmaceutical sector, chemical filter plates are employed to ensure the purity of drug formulations. They assist in the removal of impurities and particulates during the production process, which is crucial for maintaining stringent quality standards.
Chemical Manufacturing
Chemical manufacturers utilize filter plates to separate unwanted solids from liquids during production processes. This separation is vital for both quality control and operational efficiency, as it prevents equipment damage and downtime.
Food and Beverage Processing
The food and beverage industry relies on chemical filter plates to safeguard product quality. By removing contaminants, these plates help maintain the integrity of food products, ensuring compliance with health regulations.
Wastewater Treatment
In wastewater treatment facilities, chemical filter plates are essential for separating solids from effluent. This process not only purifies the water but also aids in recovering valuable resources from waste.
Oil and Gas Industry
Chemical filter plates are used in the oil and gas industry to separate particulates from drilling fluids and other liquids. This filtration process is crucial for maintaining the efficiency and longevity of equipment used in extraction and processing.
Advantages of Using Chemical Filter Plates in Industrial Settings
The adoption of chemical filter plates in industrial settings offers numerous advantages:
Improved Efficiency
Chemical filter plates enhance operational efficiency by ensuring effective filtration, resulting in reduced equipment wear and longer service life.
Cost Savings
By minimizing downtime and maintenance needs, chemical filter plates contribute to significant cost savings over time. Their durability means fewer replacements and repairs, translating to lower operational costs.
Environmental Sustainability
Effective filtration helps industries reduce waste, contributing to environmental sustainability. Chemical filter plates enable the recovery of valuable materials, reducing the need for raw material extraction and minimizing environmental impact.
Customizability
Manufacturers can customize chemical filter plates to meet specific application requirements, ensuring optimal performance in diverse industrial environments.
Maintenance and Care for Chemical Filter Plates
To ensure the longevity and effectiveness of chemical filter plates, proper maintenance is essential.
Regular Inspection
Conducting regular inspections helps identify wear and tear early, allowing for timely replacements or repairs. Inspecting for leaks, cracks, or other defects is crucial to maintaining system integrity.
Cleaning Procedures
Establishing a cleaning protocol is vital for maintaining filtration efficiency. Depending on the material, chemical filter plates may require specific cleaning agents. Following manufacturer guidelines ensures optimal performance.
Storage Recommendations
When not in use, chemical filter plates should be stored in a clean, dry environment to prevent contamination or damage. Proper storage conditions extend their service life and ensure they perform effectively when needed.
Future Trends and Innovations in Filter Plate Technology
As industries evolve, so does the technology surrounding chemical filter plates. Several trends indicate the future direction of filter plate innovations.
Smart Filtration Systems
The integration of smart technology into filtration systems is on the rise. Sensors and IoT-enabled devices can monitor filtration performance in real-time, enabling proactive maintenance and optimization.
Advanced Materials
Research into new materials promises to enhance the durability and efficiency of chemical filter plates. Innovations such as nanomaterials may provide superior filtration capabilities while being more environmentally friendly.
Sustainability Initiatives
Industries are increasingly focusing on sustainability. Future chemical filter plate designs will likely prioritize recyclable and sustainable materials, aligning with global environmental goals.
Frequently Asked Questions
1. What are chemical filter plates made of?
Chemical filter plates can be constructed from various materials, including polypropylene, polyethylene, stainless steel, and specialized polymers, depending on the application and required chemical resistance.
2. How often should chemical filter plates be replaced?
The replacement frequency of chemical filter plates depends on factors such as usage intensity and the nature of the materials being filtered. Regular inspections can help determine when replacement is necessary.
3. Can chemical filter plates be cleaned and reused?
Yes, many chemical filter plates can be cleaned depending on the material and design. However, it is essential to follow manufacturer guidelines for cleaning and maintenance to ensure optimal performance.
4. What industries benefit from using chemical filter plates?
Industries such as pharmaceuticals, food processing, chemical manufacturing, wastewater treatment, and oil and gas significantly benefit from using chemical filter plates.
5. How do chemical filter plates improve operational efficiency?
Chemical filter plates enhance operational efficiency by providing effective filtration, reducing equipment wear, minimizing downtime, and ultimately lowering operational costs.
Conclusion
Chemical filter plates are revolutionizing industrial filtration processes, offering significant benefits across multiple sectors. Their ability to enhance product quality, ensure regulatory compliance, and improve operational efficiency makes them indispensable in modern industrial applications. As technology continues to evolve, the future of chemical filter plates looks promising, with innovations aimed at sustainability and efficiency paving the way for advancements in filtration systems. By integrating these advanced solutions, industries can unlock their full potential, driving progress and improving their environmental footprint.
Contact Us
E-mail :
Ying@hsdingyuan.com
Phone/WhatsApp:
+86-13031859588
Address:
No. 104, Jingzhou Shuangchuang Industrial New Area, Jing County, Hengshui City, Hebei Province