Breaking Down the Components of a High-Quality Chemical Filter Press Part
Jun 27,2025
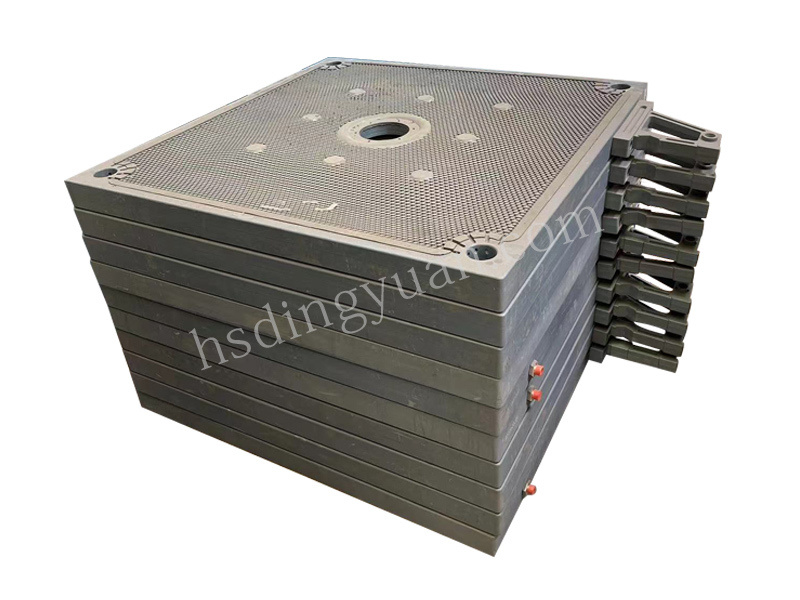
Breaking Down the Components of a High-Quality Chemical Filter Press Part
Table of Contents
- 1. Introduction to Chemical Filter Presses
- 2. Importance of High-Quality Filter Press Parts
- 3. Key Components of Chemical Filter Press Parts
- 4. Material Selection for Durability and Efficiency
- 5. Technological Advancements in Filter Press Design
- 6. Maintenance Tips for Longevity
- 7. Applications of High-Quality Chemical Filter Press Parts
- 8. Conclusion
- 9. Frequently Asked Questions
1. Introduction to Chemical Filter Presses
In industrial applications, the chemical filter press serves as a pivotal piece of equipment utilized for separating solids from liquids. This process is vital for enhancing the purity of chemical substances, complying with environmental regulations, and recycling valuable materials. Understanding the components of a high-quality chemical filter press part is essential for industry stakeholders, from manufacturers to operators.
2. Importance of High-Quality Filter Press Parts
High-quality filter press parts contribute significantly to operational efficiency and effectiveness. They ensure optimal filtration performance, reduce downtime, and ultimately lead to cost savings. Low-quality components often result in leaks, increased maintenance costs, and reduced lifespan of the equipment. Therefore, investing in top-tier parts is essential for any industrial operation relying on chemical filtration.
3. Key Components of Chemical Filter Press Parts
A chemical filter press consists of several critical components, each designed to perform a specific function in the filtration process. Understanding these components can help users make informed decisions when selecting filter press systems.
3.1 Filter Plates
Filter plates are central to the operation of a chemical filter press. Typically made from materials such as polypropylene, stainless steel, or cast iron, these components serve as the filtration medium where the separation occurs.
The design of the filter plate can vary, with options including recessed, membrane, and chamber plates. Recessed plates allow for higher capacity due to their larger volume, while membrane plates enable faster cake discharge through the application of pressure.
3.2 Filter Cloths
Filter cloths are another crucial element in achieving effective filtration. They are designed to allow liquid to pass while retaining solid particles. The choice of filter cloth is determined by several factors, including the type of slurry, desired filtration rate, and operational conditions.
These cloths can be made from various materials, including polyester, polypropylene, and nylon, and can be customized in terms of mesh size, thickness, and weave type to suit specific processes.
3.3 Frame Structures
The frame structure of a filter press supports the filter plates and provides stability during operation. Typically constructed from robust materials like carbon steel or stainless steel, the frame must withstand the pressure exerted during the filtration process.
Design considerations for the frame include ease of assembly, accessibility for maintenance, and compatibility with various filter plate sizes.
3.4 Hydraulic Systems
A hydraulic system is essential for the operation of a filter press, controlling the opening and closing of the plates. This system ensures the plates are tightly compressed during filtration while allowing for quick and efficient unloading.
Modern hydraulic systems often incorporate automated features, enhancing operational efficiency and reducing the need for manual labor.
3.5 Piping Systems
The piping system facilitates the flow of materials into and out of the filter press. Proper design and material selection for the piping are crucial to prevent leaks and ensure smooth operation.
Factors such as pipe diameter, material compatibility, and layout significantly influence the overall efficiency of the filtration process.
4. Material Selection for Durability and Efficiency
Choosing the right materials for filter press components is vital for ensuring longevity and optimal performance. Here are some key considerations:
- **Corrosion Resistance**: Given the chemical nature of the applications, materials must withstand corrosive substances without degrading.
- **Strength and Durability**: Components should withstand high pressures encountered during operation.
- **Temperature Resistance**: The materials should perform effectively at varying temperatures, especially in high-heat applications.
Investing in high-quality materials not only enhances the durability of each component but also improves overall system efficiency.
5. Technological Advancements in Filter Press Design
The filter press industry has seen significant technological advancements aimed at improving efficiency and reducing operational costs. Key innovations include:
- **Automated Controls**: Modern filter presses often come with automated control systems that monitor and adjust parameters in real time, enhancing operational efficiency.
- **Smart Filter Presses**: These systems integrate IoT technology, allowing for remote monitoring and predictive maintenance, ultimately reducing downtime.
- **Advanced Materials**: The introduction of high-performance materials, such as composite materials, has improved the durability and performance of filter press components.
These advancements not only streamline operations but also reduce labor costs and improve safety.
6. Maintenance Tips for Longevity
Regular maintenance of chemical filter press parts is essential to ensure optimum performance and longevity. Here are some practical maintenance tips:
- **Routine Inspections**: Regularly check all components for signs of wear and tear, particularly the filter cloths and plates.
- **Cleaning Procedures**: Establish a cleaning routine for the filter press to prevent clogging and maintain filtration efficiency.
- **Lubrication**: Ensure that all moving parts, especially those in hydraulic systems, are adequately lubricated to prevent wear.
- **Monitoring Performance**: Keep track of filtration rates and operational parameters to identify any deviations from normal performance.
Implementing these maintenance practices can significantly extend the lifespan of your filter press.
7. Applications of High-Quality Chemical Filter Press Parts
High-quality chemical filter press parts find applications across various industries, including:
- **Food and Beverage**: Used for juice clarification and wine filtration.
- **Pharmaceuticals**: Essential for solid-liquid separation in drug manufacturing.
- **Mining**: Utilized to dewater mineral slurries.
- **Wastewater Treatment**: Effective in treating industrial wastewater before discharge.
Each application requires specific considerations regarding component selection and operational parameters, further emphasizing the importance of high-quality parts.
8. Conclusion
Understanding the components of a high-quality chemical filter press is crucial for industry professionals seeking to optimize filtration processes. By focusing on the key parts—filter plates, filter cloths, frame structures, hydraulic systems, and piping systems—users can make informed decisions that greatly enhance operational efficiency. Additionally, advancements in technology and material science continue to pave the way for superior performance in chemical filtration applications. Investing in quality not only ensures better performance but also extends the life of the equipment, resulting in significant cost savings in the long run.
9. Frequently Asked Questions
1. What is the primary function of a chemical filter press?
The primary function of a chemical filter press is to separate solids from liquids in a slurry, enhancing purification and recovery processes in various industrial applications.
2. How often should filter press components be inspected?
Filter press components should be inspected regularly, ideally every few months, or more frequently depending on the operational conditions and frequency of use.
3. What are the signs of a failing filter cloth?
Signs of a failing filter cloth include reduced filtration rates, increased cake moisture content, and visible tears or wear in the fabric.
4. Can filter presses handle high-temperature applications?
Yes, filter presses can be designed to handle high-temperature applications, but careful selection of materials and components is essential for optimal performance.
5. What maintenance practices can extend the life of a filter press?
Regular inspections, cleaning procedures, lubrication of moving parts, and performance monitoring can all help extend the life of a filter press.
Contact Us
E-mail :
Ying@hsdingyuan.com
Phone/WhatsApp:
+86-13031859588
Address:
No. 104, Jingzhou Shuangchuang Industrial New Area, Jing County, Hengshui City, Hebei Province